Projekty Krajowe
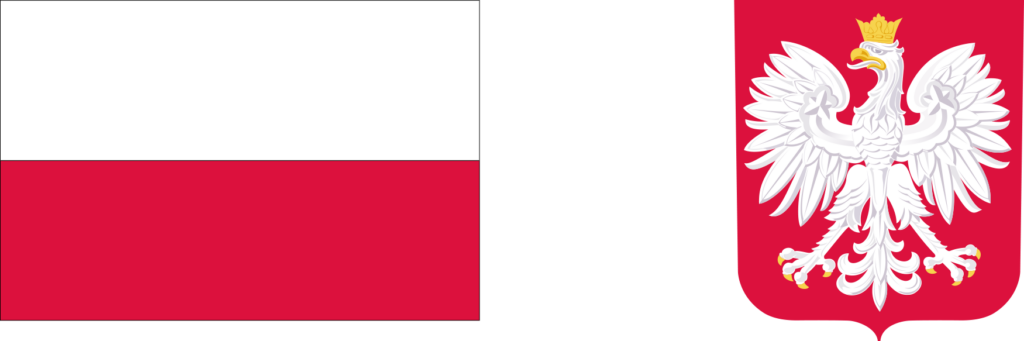
Projekt „Materiały termoizolacyjne na bazie surowców alternatywnych do zastosowań w budownictwie modułowym” (PB_Evotherm) jest dofinansowany z dotacji celowej Prezesa Centrum Łukasiewicz.
Całkowita wartość projektu: 2 277 610,38 PLN
Dofinansowanie: 2 049 849,34 PLN
Projekt dotyczy opracowania metody i wytworzenia nowoczesnych materiałów izolacyjnych w postaci uniepalnionych pianek poliuretanowych powstałych na bazie surowców odnawialnych bądź surowców pochodzących z recyklingu. Opracowany materiał znajdzie zastosowanie w budownictwie modułowym do termoizolacji ścian oraz dachów nowowznoszonych budynków. Tematyka projektu obejmuje nowe, zrównoważone dla gospodarki technologie dla budownictwa modułowego obejmujące dywersyfikację bazy surowcowej do produkcji poliuretanów. Kluczowym elementem projektu są lekkie izolacje termiczne bazujące na piankach poliuretanowych, które wśród dostępnych materiałów izolacyjnych, tj. spienionego polistyrenu (EPS), wełny mineralnej lub celulozy, wykazują najlepsze właściwości pod kątem izolacji termicznej oraz izolacji akustycznej. Niestety, wśród wymienionych materiałów charakteryzują się najwyższym kosztem produkcji oraz nie są materiałami “przyjaznymi dla środowiska”. Celem Projektu jest opracowanie 2 typów materiałów izolacyjnych: pianek sztywnych do zastosowania jako warstwa izolacyjna ścian i elewacji oraz formulacji natryskowej, służącej do izolacji dachów lub “reizolacji” starych pokryć dachowych wraz z likwidacją mostków cieplnych. Kluczowym elementem projektu jest również dobór antypirenów, które pozwolą na spełnienie wymogów dotyczących palności opracowywanych materiałów. Do wytwarzania sztywnych pian izolacyjnych przewiduje się wykorzystanie co najmniej 30% składnika polieterowego pochodzącego z depolimeryzacji materiałów odpadowych: izolacji cieplnych rur i przewodów oraz odpadowych pianek elastycznych pochodzących z przemysłu meblarskiego. Tego typu odpady są trudne do przetworzenia metodą mechaniczną i chemiczną. Charakteryzują się bardzo małą gęstością, co wymaga kompresji materiału oraz specjalistycznych urządzeń do rozdrabniania. Obecnie odpady z przemysłu meblarskiego są rozdrabniane mechanicznie i dodawane w trakcie procesu spieniania, jednakże materiały zanieczyszczone lub o ciemnej barwie nie mogą być dodawane do pianek tapicerskich. Dlatego też, w celu zagospodarowania szerokiego wachlarza odpadów poliuretanowych zostanie przeprowadzona chemiczna depolimeryzacja z wykorzystaniem alkoholi z dwoma grupami hydroksylowymi, oczyszczenie płynnego produktu depolimeryzacji oraz opracowanie formulacji, które będą dostosowane do jakości otrzymanego recyklowanego poliolu. Jednym z elementów Projektu będzie również opracowanie uniwersalnej metody mechanicznego rozdrabniania odpadów poliuretanowych, w bez konieczności rozdzielania tworzyw spienionych typu: moulded, flexible oraz rigid. Pianki zostaną rozdrobnione do uziarnienia 5-10mm, skompresowane próżniowo, a następnie przekazane do procesu glikoly w celu ich chemicznej dekompozycji. Obecne wyniki wskazują, iż glikoliza tworzyw PUR pozwala na uzyskanie produktu o ciemnej barwie, lepkości kinematycznej w zakresie 200-1500 cSt. oraz liczbie hydroksylowej w zakresie 400-600 mg KOH/g, co jest zgodne z wymaganiami dla składnika polieterowego stosowanego w piankach poliuretanowych sztywnych. Zgodnie ze sztuką, niezbędne będzie stosowanie polieterów o liczbie hydroksylowej ok. 50 mg KOH/g, oraz dodatków uszlachetniających, jak katalizatory i surfaktanty regulujące strukturę porów. Elementem Projektu będzie również opracowanie dwuskładnikowej formulacji izolacji przeznaczonej do natrysku w miejscu montażu, lub w istniejących już budynkach. Tego typu izolacje cieszą się obecnie dużym zainteresowaniem, ponieważ poliuretany charakteryzują się bardzo dobrymi właściwościami penetrującymi oraz bardzo wysoką adhezją do podłoża, co pozwala na aplikację w dowolnym, nawet trudno dostępnym miejscu, zapewniając szczelną izolację termiczną i likwidację mostków termicznych. Celem Projektu będzie opracowanie biopolioli na bazie odpadowej gliceryny powstającej w procesie produkcji biodiesla oraz posmażalniczych olejów roślinnych, które po odpowiedniej modyfikacji będą mogły zastąpić komponent polieterowy. Kluczowymi parametrami pian otrzymanych z udziałem powyższych polioli będzie zachowanie wysokiej adhezji do podłoża oraz zapewnienie zakładanej izolacyjności termicznej dzięki ich odpowiedniej strukturze. Istotnym elementem niniejszego projektu jest także otrzymanie antypirenów fosforanowych, które to stanowić będą komponent otrzymywanych materiałów termoizolacyjnych. Ich rola w produkcie końcowym jest niezwykle istotna, gdyż polega na polepszeniu parametrów przeciwpożarowych uzyskanego produktu, przy jednoczesnym zachowaniu parametrów użytkowych otrzymanych pianek. Wspomniane antypireny fosforowe będą chemicznie wbudowane w strukturę materiału izolacyjnego, przez co podczas długotrwałego użytkowania nie będą ulegały ulotnieniu. Ostatnim etapem Projektu będzie wydanie dla opracowanych pian Krajowej Oceny Technicznej, która pozwoli na wprowadzenie innowacyjnego materiału termoizolacyjnego do obrotu na rynku krajowym.